随着社会的发展,更多人追求一种更加“绿 {MOD}”的生活方式。那么非常明显的,电动车将会在汽车行业快速发展。因为电动车载着我们来来回回的往返于工作和超市之间时,可以达到更少的或者零尾气排放,消耗更加少的能源。
然而,电动车是汽车工业方面的一个典型转变——新的驱动系统,新的技术,新的测试方案等等。随着电子工业车辆的增长,这种交通工具给工业带来了新的测试测验的挑战。
汽车工业已经接受了未来的大多数混合动力和插电式混合动力车使用锂离子电池作为动力能源。这种电池需要一个精心设计的充电系统,来保证电池的寿命和安全。这就意味着,电动车的BMS(the Battery Management Systems)系统问题的有效测试是主要挑战之一——电子工业需要设法保持电池可以储存高等级的能量来驱动电车。
为了帮助完成BMS系统的测试、DMC的工程师和软件工程师与pickering公司合作,为主要的生产商提供BMS测试系统的解决方案。这种解决方案是基于PXI模块的电池系统仿真。在本文中,我们将会讨论到一些必要的测试和为什么必须要有这些测试。我们也会展示在这样的系统中是怎样利用PXI的及其对于这么复杂的问题PXI为什么是一个完美的解决方法。
一.构建和测试一个BMS系统
为达到BMS系统对电池更先进更稳定的需求,锂离子电池的制作工艺发生了高度的内在变化。通过快速的监视和平衡每个电池组的电荷状态(SOC),BMS系统必须能够模拟每一个正在模块中工作的电池组。堆栈式电池设计可以无限制的组合好的和坏的单元,并且可以适应大多数环境。这些变化和使用场景使电池组的仿真和有效的电池模拟系统成为必要,BMS是可以在产品的生产环境中测试模拟电池组顺利使用的方案。
因此BMS系统成为了HEV(Hybrid-Electric Vehicle)、EV和PHEV(Plug-In Electric Vehicle)电动拖动装置中的关键部件。典型的BMS系统控制ESS(Energy Storage System)的所有功能,包括了电池组电压和电流监视,电池电压测量,电池电压平衡,计算电池组的充电状态,电池温度和健康监视,这样就可以保证全部电池组的安全和性能最优化。
BMS模块和相关的代替模块必须从电池组中通过相关温度、电流、电压的传感器模块中读取电压和输入参数。从这里,BMS系统必须处理这些参数,并且做出逻辑判断来控制电池组的性能和安全,并且还要通过模拟的、数字的和输出交流,时刻反馈输入状态和工作状态。
BMS系统的有效测试涉及两个主要功能,第一:精确的模拟传感器和电池组的输入信号;第二:测量、收集并且处理BMS系统处理后的数字和模拟信号的结果。
二.为什么BMS系统极具挑战性
主要有两个原因分别的验证了电池组BMS系统的优越性能。包括安全性和长寿。
很多人都听说过关于锂离子电池在笔记本和手机中爆炸的恐怖故事。好消息是锂离子电池拥有6倍于铅酸电池的能量密度,3倍于镍-金属氢化物电池的能量密度,另外,电池组拥有更大的被回收利用的空间。但是为了增强可用性,每次你把更多的能量压缩进这么小的一个空间,安全隐患有可能增加。
受控的电池能源的释放通过电流电压的形式提供电能。不受控的电池能源释放可以导致有毒物质的释放(比如有毒烟雾),产生火花,高压事件(比如爆炸),或者这些任意的组合。所有的锂离子系统都是使用一种电解液,这种电解液易燃,并且有倾向于“热失控”。当你对这种材料加热,它会达到起振温度,然后开始对自己加热,最终导致起火或者爆炸。
不受控的电能释放可以引起严重的损害,比如如碰撞、刺穿或燃烧,这些虽然可以通过机械安全装置和合适的结构设计来缓和,但是这些现象也可以有电池短路、反常的高耗电功率、形成过热、过度充电或者经常的再充电引起,这些都可以使电池老化。正确的设计和验证电子安全监控系统,是预防这些事故最好的方法,换句话说就是BMS。
BMS可以跟踪电池组的精确电池电荷状态,这样可以维持吃紧的电池寿命。电池过冲过放会严重影响它的使用寿命。因此,BMS必须包括一个精确的充电检测功能。因为,我们不能直接的测量电池的充电过程,充电百分比必须通过测量一些具体的特征计算出,比如电压,温度,电流或者其他的参数。BMS系统可以用来测量和计算这些参数的。验证BMS系统对电荷状态计算的精确性对电池组性能和长寿命是至关重要的。
三.电池组仿真
锂离子电池有一个磷酸铁锂阴极和一个石墨阳极,标示了3.2V的开路电压和典型的充电电压3.6V。镍钴锰酸锂(NMC)氧化物阴极和石墨阳极标示了3.7V的电压,最大充电电压4.2V。一个典型的汽车专用的电池串联了96个电池模块,有能力产生超过350V的电压。高电压与低电压相比,允许能量通过较细的线缆转化到驱动系统,损失更少的能量。但是,如果要避免损坏电子系统,高电压就需要精细化管理。在真实的电池组中测试和验证新的BMS系统不是一个可行的解决方法。因为一个错误有可能导致非常严重的损坏,也可能伤到测试员。测试也不可以一遍又一遍的重复执行。只有当非常有信心的时候才可以把BMS连接到真正的电池组中。另一个问题是故障和实际的电池组的特征不能多样化的模拟BMS可以处理的情形。故障注入的时候,尤其在产品开发研制阶段,对成功验证硬件和软件的设计是否可靠是非常重要的。
DMC与pickering合作,要求电池模拟系统可以模拟低电压电池组,来验证BMS系统的可行性。电池组的每一个电池模块输出电压都是编程好的,并且电池组必须有能力处理充放电状态。
四.设计挑战
Pickering公司已经有在移动应用方面设计单槽的PXI电池模拟模块的经验。所以,接下来一个可行性的设计开始进行了。为了保持系统的简洁和低成本,最后决定我们需要尽可能的把更多的通道设计到一个模块里面。而且,这个产品价格应用于汽车行业还是合理的。
并不是消极的说,设计高密度、多单元的电池模拟器,PXI并不是理想的平台,但也并不是不可能,不过模块的设计的确会限制某些功能。然而,所有PXI模块处理这种测试的可用性和PXI被广泛的接受,这就表示我们必须专注于PXI的解决方案。
很明显的,最终产品必须使用起来更加可靠、简洁、安全。一个PXI机箱通常可以支持多大18个外围槽位。所以设计简洁的结构的要求就需要每个槽位可以模拟6个单元的电池组——一个机箱的16个模块可以模拟96个电池组。这种密度限制了每个电池的设计。这种要求很难达到最终用户的项目时间要求。所以大部分的组件必须是现成的可利用的。
每个单元都必须有能力提供高达300mA的电流和形成超过4.2V的电压。机箱背板为每个槽位和整个系统提供足够的能源,这对机箱背板来说是一个重要的挑战—–值得注意的是我们还需要瞬态响应来模拟电池。
PXI背板可以提供为每个模块提供6A电流和5V的电压—–到目前为止,大部分的PXI背板都有这个能力。然而,总所周知5V的DC变换的效率非常低,设计产品的时候就要考虑巨大的能量损耗,这些能量损耗会造成机箱严重发热。解决这个问题的方案是,给内部模块供电以+5V为主,以+12V和-12V来作为补充。
通过一个快速线性稳压器,每一个电池仿真模块单元使用单独固定的DC–DC变换来分别供电,。快速线性稳压器要求允许电池在模拟的时候可以不使用低压调整,也可以不使用过大的输出解耦电容。
在最坏的情况下,所需的线性稳压器可以使大量的能量散发出去。但是,很明显的,在模块里面的每个电池都非常受限于空间,这就会反过来限制稳压器的散热效果。解决这个问题的办法是使用汽车专用的可以抵抗高温的、装入热保险丝的和用铜覆盖PCB表面的特殊设计的稳压器。在PXI机箱中,有效率的冷却系统保证了PCB表面的空气流动—–PXI标准的另一个方面,当激活装置安装到PXI模块的底部的时候,可以很好地在这种应用类型下工作。
安全性和绝缘性也是重大的设计挑战。在电池模块中,96个单元串联在一起,如果每个单元都输出标示的电压4.2V,那么将会导致输出高达致命的输出电压。隔离层必须设计成可以抵抗大于两倍的模块单元间的电压,目前还是采用程序控制的电池模块。有一个方案是使用数字的光电隔离器来给PXI背板提供控制接口,保险连锁装置定义允许使用者提供这种方式连接模块,如果使用者没有使用线缆连接PXI的前面板,那么整个系统将会关闭。
BMS系统也需要仿真电池充电的过程。BMS必须可以有能力两者兼顾,但是要求的反向电流往往比源电流小得多。这个问题通过在设计中添加可以提供预加载电源的集成的可编程电流负荷来解决。当BMS正在充电时,电流负荷可以保证源电流电源的供应。
所有的这些挑战和解决方案被评估之后,pickering公司提议设计组合一个新的6通道的电池模拟模块来达到DMC的要求。经过双方交流,修改设计和问题澄清的预期性能之后,现在DMC已经下单预定这种电池仿真模块。
五.Pickering公司在这种测试系统设计与实现
Pickering公司不断的改进这个设计方案,最后设计了第一个模块。就是现在的41-752模块。这种调整不仅仅局限于硬件设计,还有测试方面等方面的挑战。rt软件支持团队与硬件设计团队同时工作生产首个有能力的测试模块硬件和二次开发软
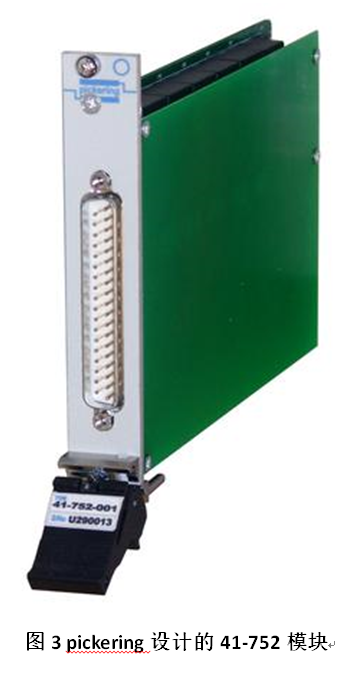
件,包括手工软面板,通过手工面板使用者可以控制每个模块中的每个电池。
直到这个模块表现出出 {MOD}的性能,
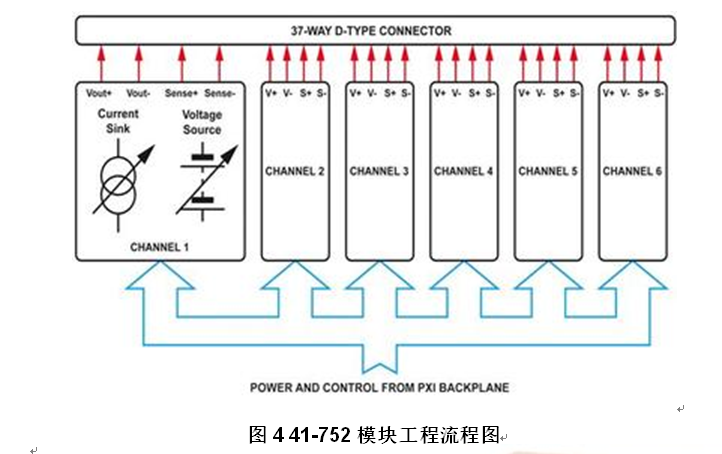
pickering将生产的其他模块寄给了DMC。DMC把这种解决方案整合进了他们的测试系统,然后发送给最终用户。经过成功的尝试和一些小的设计调整,用户开始购买这种模块,从此商业领域便有了41-752模块。
现在市场上是可以购买到41-752模块的,
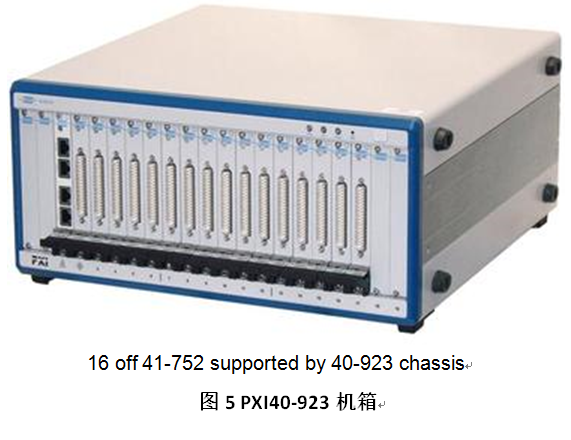
它支持6通道7V电压、300mA电流的电池模拟仿真。高电压隔离层最高可承受750V,允许通过D-Type串联更多的电池单元。一个灵活的安全锁装置可以保证系统可以非常安全的运行。Pickering的40-923机箱可以支持大功率模块,它就可以提供足够大的电压和电流来达到仿真高达108个电池单元的要求。
六.PXI在其他测试领域的应用
除了电池模拟仿真之外,PXI模块还可以模拟温度传感器、数字和模拟I/O口、电池组输出端的高电压和BMS与CAN口之间的通讯。系统由外两个PXI机箱和外部电路组成。整个系统非常的紧凑,被嵌入一个1.5米的架子中,
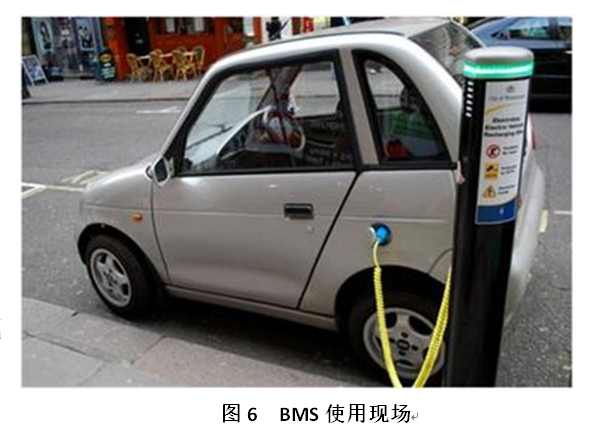
完全达到了客户的需求。
七.总结
在未来几年,我们将会在道路上看到越来越多的混合动力或者电力的电动车。为了保证电池的寿命和防止系统的损害,BMS是一个非常好的选择。将会非常满足客户的测试要求。PXI测试系统做到体积更小、费用更低、更加安全可靠。
更多PXI、PCI开关、故障注入资料请联系wsj@hkaco.com
原文地址:
http://wiki.pickeringtest.net/Developing+a+Battery+Management+Test+System?__hstc=256762388.26e3605660464ca01b1036db865f2fae.1409970954151.1414928196839.1414971041192.39&__hssc=256762388.2.1414971041192&__hsfp=205712518